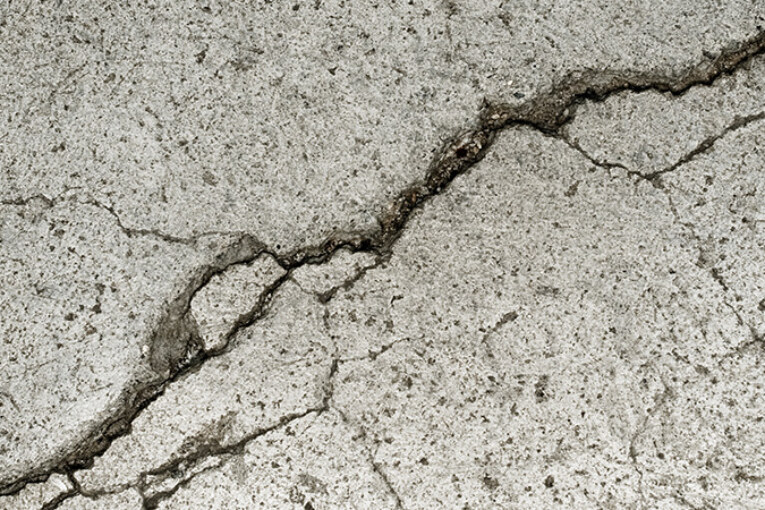
About
Concrete is a composite material composed of fine and coarse aggregate bonded together with a fluid cement (cement paste) that hardens over time. Most concretes used are lime-based concretes such as Portland cement concrete or concretes made with other hydraulic cements, such as calcium aluminate cements. However, asphalt concrete, which is frequently used for road surfaces, is also a type of concrete, where the cement material is bitumen, and polymer concretes are sometimes used where the cementing material is a polymer.
When aggregate is mixed together with dry Portland cement and water, the mixture forms a fluid slurry that is easily poured and molded into shape. The cement reacts chemically with the water and other ingredients to form a hard matrix that binds the materials together into a durable stone-like material that has many uses. Often, additives (such as pozzolans or superplasticizers) are included in the mixture to improve the physical properties of the wet mix or the finished material. Most concrete is poured with reinforcing materials (such as rebar) embedded to provide tensile strength, yielding reinforced concrete.
Concrete production
Concrete production is the process of mixing together the various ingredients—water, aggregate, cement, and any additives—to produce concrete. Concrete production is time-sensitive. Once the ingredients are mixed, workers must put the concrete in place before it hardens. In modern usage, most concrete production takes place in a large type of industrial facility called a concrete plant, or often a batch plant.
In general usage, concrete plants come in two main types, ready mix plants and central mix plants. A ready mix plant mixes all the ingredients except water, while a central mix plant mixes all the ingredients including water. A central mix plant offers more accurate control of the concrete quality through better measurements of the amount of water added, but must be placed closer to the work site where the concrete will be used, since hydration begins at the plant.
A concrete plant consists of large storage hoppers for various reactive ingredients like cement, storage for bulk ingredients like aggregate and water, mechanisms for the addition of various additives and amendments, machinery to accurately weigh, move, and mix some or all of those ingredients, and facilities to dispense the mixed concrete, often to a concrete mixer truck.
Modern concrete is usually prepared as a viscous fluid, so that it may be poured into forms, which are containers erected in the field to give the concrete its desired shape. Concrete formwork can be prepared in several ways, such as Slip forming and Steel plate construction. Alternatively, concrete can be mixed into dryer, non-fluid forms and used in factory settings to manufacture Precast concrete products.
Workability
Workability is the ability of a fresh (plastic) concrete mix to fill the form/mold properly with the desired work (vibration) and without reducing the concrete’s quality. Workability depends on water content, aggregate (shape and size distribution), cementitious content and age (level of hydration) and can be modified by adding chemical admixtures, like superplasticizer. Raising the water content or adding chemical admixtures increases concrete workability. Excessive water leads to increased bleeding or segregation of aggregates (when the cement and aggregates start to separate), with the resulting concrete having reduced quality. The use of an aggregate blend with an undesirable gradation can result in a very harsh mix design with a very low slump, which cannot readily be made more workable by addition of reasonable amounts of water. An undesirable gradation can mean using a large aggregate that is too large for the size of the formwork, or which has too few smaller aggregate grades to serve to fill the gaps between the larger grades, or using too little or too much sand for the same reason, or using too little water, or too much cement, or even using jagged crushed stone instead of smoother round aggregate such as pebbles. Any combination of these factors and others may result in a mix which is too harsh, i.e., which does not flow or spread out smoothly, is difficult to get into the formwork, and which is difficult to surface finish.
Durability
Durability of concrete may be defined as the ability of concrete to resist weathering action, chemical attack, and abrasion while maintaining its desired engineering properties.
Durability is defined as the capability of concrete to resist weathering action, chemical attack and abrasion while maintaining its desired engineering properties. It normally refers to the duration or life span of trouble-free performance. Different concretes require different degrees of durability depending on the exposure environment and properties desired. For example, concrete exposed to tidal seawater will have different requirements than indoor concrete.
Concrete will remain durable if:
- The cement paste structure is dense and of low permeability.
- Under extreme condition, it has entrained air to resist freeze-thaw cycle.
- It is made with graded aggregate that are strong and inert.
- The ingredients in the mix contain minimum impurities such as alkalis, Chlorides, sulphates and silt.
Types of Durability
There are many types but the major ones are:
- Physical durability of concrete
- Chemical durability of concrete
#Physical Durability of Concrete
Physical durability is against the following actions:
- Freezing and thawing action.
- Percolation / Permeability of water.
- Temperature stresses i.e. high heat of hydration.
#Chemical Durability of Concrete
Chemical durability is against the following actions:
- Alkali Aggregate Reaction.
- Sulphate Attack.
- Chloride Ingress.
- Delay Ettringite Formation.
- Corrosion of reinforcement.
Factors affecting durability of concrete
Durability of Concrete depends upon the following factors:-
#Cement content
Mix must be designed to ensure cohesion and prevent segregation and bleeding. If cement is reduced, then at fixed w/c ratio the workability will be reduced leading to inadequate compaction. However, if water is added to improve workability, water / cement ratio increases and resulting in highly permeable material.
#Compaction
The concrete as a whole contain voids can be caused by inadequate compaction. Usually it is being governed by the compaction equipments used, type of formworks, and density of the steelwork.
#Curing
It is very important to permit proper strength development aid moisture retention and to ensure hydration process occur completely.
#Cover
Thickness of concrete cover must follow the limits set in codes.
#Permeability
It is considered the most important factor for durability. It can be noticed that higher permeability is usually caused by higher porosity. Therefore, a proper curing, sufficient cement, proper compaction and suitable concrete cover could provide a low permeability concrete.
Causes for the Lack of Durability in Concrete
1. External Causes:
- Extreme Weathering Conditions
- Extreme Temperature
- Extreme Humidity
- Abrasion
- Electrolytic Action
- Attack by a natural or industrial liquids or gases
2. Internal Causes
a) Physical
- Volume change due to difference in thermal properties of aggregates and cement paste
- Frost Action
b) Chemical
- Alkali Aggregate Reactions
- Alkali Silica Reaction
- Alkali Silicate Reaction
- Alkali Carbonate Reaction
- Corrosion of Steel