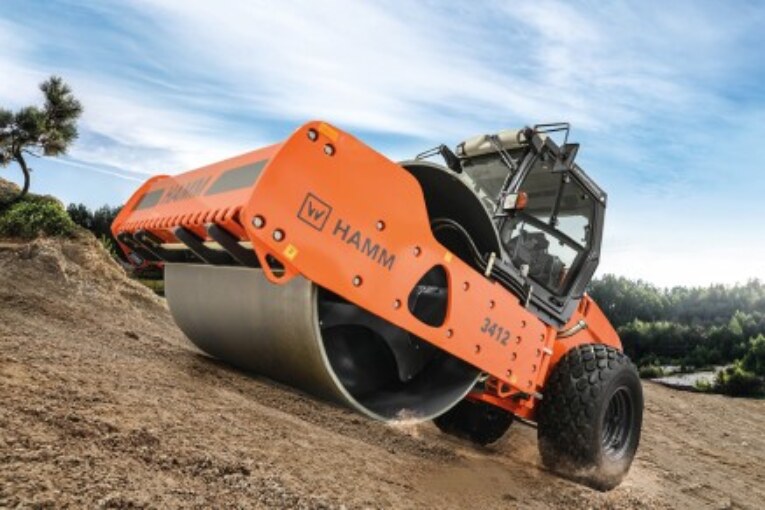
What are the most important criteria to be considered? What methods need to be applied? What machines used?
NEW ROAD CONSTRUCTION
The construction of a new road – whether from asphalt or concrete – requires the production of an excellently bonded pavement structure, beginning with a stable base layer and going all the way to a precisely leveled surface course.
What are the most important criteria to be considered? What methods need to be applied? What machines used?
1).Construction of base layers
The base layer of a road lays the foundation for the upper pavement structure. It must offer excellent bearing capacity, be capable of withstanding a broad range of different climatic conditions, and remain functional over several decades. What materials are used for the construction of base layers? What properties do they need to possess?
i. A strong base for the upper road structure
The bottom layer essentially comprises an unbound mixture of coarse and fine crushed stone, as well as crushed sand, to achieve the desired load-bearing capacity and absorb traffic loads so that the underlying sub grade is not deformed.
ii. A gravel layer protects against frost
Roads are exposed to particularly high stresses when the water contained in the pavement structure begins to freeze. Water expands when freezing, which can lead to frost damage that will sooner or later have an impact also on the road surface. This is prevented by a so-called frost blanket which usually consists of a mixture of gravel and sand, supplemented by crushed mineral aggregate. When compacted, these layers of frost-resistant materials conduct water away from the upper pavement layers, reducing tensions very effectively at the same time.
Compacting a gravel base layer using a single-drum compactor from HAMM.
Compacting a gravel base layer using a single-drum compactor from HAMM.
iii.The mix makes all the difference
In many cases, a bound base course is overlaid over the unbound base course. Bitumen, cement or lime is predominantly used as binder.
Placing a base layer with a Vajgele road paver.
Placing a base layer with a Vogele road paver.
iv.Bituminous bound base layers
Mixes containing bitumen are referred to as hot-paved or cold-paved asphalt base courses, depending on whether the mix is hot or cold. The base course is said to be hydraulically bound when cement or lime is used as binder.
v.Hydraulically bound base layers
When the mineral aggregate mixture is bound with cement or lime, the resulting base layer is called a hydraulically bound base layer. Mineral aggregate mixtures used for this type of base layer consist of uncrushed gravel or coarse aggregate, chippings, and crushed or natural sand. Ever more frequently, these mixes also contain a percentage of recycled construction materials.
Paving a hydraulically bound base layer. Precisely metered quantities of cement slurry are added via hose connections from the slurry mixer to the cold recycler.
Paving a hydraulically bound base layer. Precisely metered quantities of cement slurry are added via hose connections from the slurry mixer to the cold recycler.
2) Asphalt paving
i. Many steps pave the way
The first person in the paving team, however, is the truck driver who fills the asphalt into the paver’s hopper. Two mutually independent conveyors transport the material through the machine to the rear, where it is uniformly distributed between paver and screed by two individually controlled rotating screw conveyors. When paving a standard mix, the temperature should always remain above 110 °C in order to ensure sufficient time for compaction.
Large-scale construction projects can be completed swiftly and asphalt pavements laid seamlessly across the greatest widths with a laydown rate of up to 1,600 t/h and a pave width of up to 16 m.
Large-scale construction projects can be completed swiftly and asphalt pavements laid seamlessly across the greatest widths with a lay down rate of up to 1,600 t/h and a pave width of up to 16 m.
ii. Supply of mix and job site logistics
The hot mix should be covered when delivered by charging trucks to ensure that the paving operation is carried out in the most suitable time frame. To guarantee continuous paving, the capacity of the asphalt mixing plant always needs to be higher than the paver’s lay down capacity. If the paver stops moving due to lack of material, disruptive lateral joints occur as a result of the paved layer cooling down. When paving standard mix, the paving temperature should be higher than 110°C to allow an as large time frame as possible for compaction.
A continual material flow and the correct set-up of the machine are two crucial factors in any paving operation.
A continual material flow and the correct set-up of the machine are two crucial factors in any paving operation.
iii.Paving with the road paver
All paving units need to be heated prior to commencing the paving operation to prevent the mix from sticking to sensitive parts of the machine. On modern pavers, the compacting systems in the screed can be actuated separately. Particularly the high compaction screeds achieve very good compaction. As a result, the rollers behind the paver require fewer passes to achieve the specified final degree of compaction.
iv.Optimum final compaction
Compaction effected by the high-density screed enables the rollers which follow behind the paver to achieve the overall final density specified by the client in fewer roller passes. In most cases, the road paver is geared for either high density or fast advance speed, both of which have an effect on the number of roller passes required.
HAMM rollers ensure the optimum final compaction of the individual asphalt courses.
HAMM rollers ensure the optimum final compaction of the individual asphalt courses.
3) Asphalt compaction
Compaction is the final procedure in road construction, its goal being to produce a surface texture of high quality. What aspects need to be considered in asphalt compaction? When compacting an asphalt road, what impact will the road’s location or ambient temperatures have on the compacting operation?
i. Packing strength into the asphalt road
What type of mix will be compacted, and what are the thicknesses of the individual layers? Where’s the job location? On a motorway, in a residential area, on a bridge? The answers to these questions will determine the type of roller to be used for compaction. What will be the paving width and paving speed? That will determine the number of rollers to be used.
ii. Getting the rollers ready
Rollers are heavy road construction machines used for compacting hot and therefore flexible asphalt pavements. To prevent them from causing damage to the new asphalt surface, they must not come to a halt during the compacting operation. For precisely that reason, machine maintenance is of particular importance. In addition to that, checks need to be carried out prior to commencing work to make sure that the drum is clean, that fuel and engine oil are available in sufficient quantities, and that the water tank has sufficient water for the drum spray system.
Combination rollers from Hamm – like the roller of the HD series shown here – offer an ideal mix of static and dynamic compaction.
Combination rollers from HAMM – like the roller of the HD series shown here – offer an ideal mix of static and dynamic compaction.
iii. The effect of temperature on the compaction result
Basically, compaction becomes more effective with increasing temperature of the paved mix. The most advantageous temperature range depends on the composition of the mix, the thickness of the pavement and the type of binder used.
iv.The different roller passes
The roller operator starts compaction at the tie-in points and follows the edge of the road from there. The pavement is pressed home in a further pass. Dynamic compaction is mainly used for the main compaction process. The drums vibrate horizontally (oscillate) or vertically (vibrate), thus significantly increasing the effect of compaction. The operation is completed by a final roller pass that will “iron out” any remaining irregularities in the asphalt pavement or surface to produce a perfect surface finish.
4) Inset concrete paving
Concrete is a particularly durable material and eminently suitable for roads which have to withstand high loads.
i.Building concrete pavements with modern road construction plants
The following sequence of operations is typical of inset paving: First of all, trucks unload the concrete in front of the paver. The slipform paver then spreads the concrete over the full paving width with its auger or spreading plough and forms the concrete profile for the roadway with the slipform mould. HF vibrators inside the slipform vibrate at high frequency, expelling air from the concrete and hence compacting it.
With larger slipform pavers, the spreading plough distributes the concrete across the entire working width
With larger slipform pavers, the spreading plough distributes the concrete across the entire working width
ii. On dowel bars, tie bars and joints
The slipform paver keeps moving all the time during the paving operation, its working speed ranging from 1 to 2 m per minute. At the same time, the paver can also insert dowel bars or tie bars in the fresh concrete. These bars reinforce the concrete. Slots are subsequently cut into the concrete pavement above the reinforcements. These slots ensure that the cracks which are invariably produced as a result of stresses and temperature fluctuations are diverted into the concrete pavement in a controlled manner.
The side tie bar inserter drives tie bars laterally into the concrete slab
The side tie bar inserter drives tie bars laterally into the concrete slab.
iii. A burlap drag finish produces the required grip
The roadway is levelled by finishing beams and super-smoothers. An entrained piece of sackcloth often ensures a non-skid surface texture. A curing unit is normally used to apply a dispersion to the fresh concrete so that the concrete cures uniformly.
Applying a liquid curing compound prevents premature and uneven drying of the concrete pavement.
Applying a liquid curing compound prevents premature and uneven drying of the concrete pavement.
5) Offset concrete paving
Instead of placing pre-fabricated concrete parts in a manual operation, the required profiles can also be produced by slipform pavers in offset application. What applications can offset concrete paving be used for? What are the advantages of slipform paving when compared to manual construction?
i. Slipform special jobs like bicycle paths, traffic barriers or kerbs
For offset slip forming, material is normally transferred to the filling hopper from a concrete mixer truck. This material is transferred to the offset slipform mounted on the side of the paver by either a pivotable conveyor belt or a pivotable screw conveyor. The slipform produces the monolithic profile as the offset paver moves forward. The range of possible shapes and sizes is immense, from such common shapes as the New Jersey profile to customized solutions.
In lieu of pre-fabricated concrete parts: rainwater gutter produced with the slipform paving method.
In lieu of pre-fabricated concrete parts: rainwater gutter produced with the slipform paving method.
ii. Economically efficient method
Offset applications extend from roadway edgings and crash barriers with a maximum height of 2 m to narrow paths. Offset paving is quick and efficient when compared to manual placement of prefabricated elements.